Von Smartphones und kabellosen Ohrhörern bis hin zu Elektrofahrzeugen liegt die treibende Kraft hinter unzähligen modernen Innovationen in einem verborgenen Helden:gesinterte Neodym-Eisen-Bor-Magnete (NdFeB)Diese Hochleistungs-Permanentmagnete verdanken ihre außergewöhnlichen magnetischen Eigenschaften einem kritischen Herstellungsschritt – dem Sintern. Dieser Artikel befasst sich eingehend mit dem Vorsinterprozess von NdFeB-Magneten und zeigt, wie sich Rohstoffe in das Rückgrat modernster Technologien verwandeln.
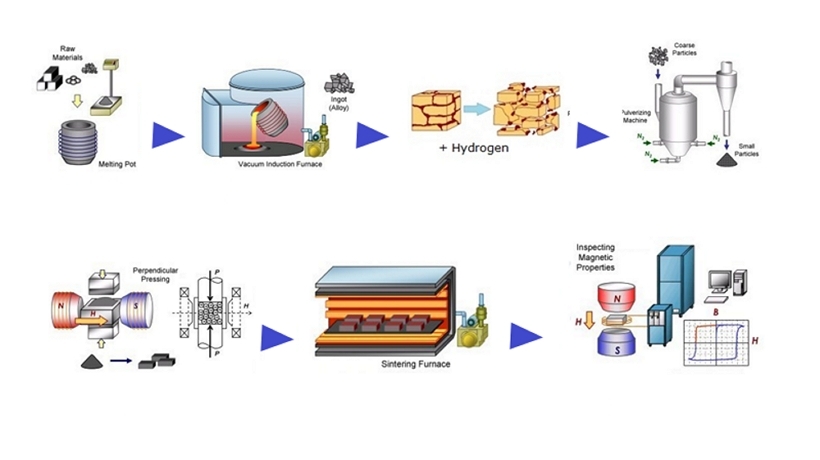
Was ist Sintern?
Sintern ist eine Materialherstellungstechnik, bei der pulverförmige Substanzen durch kontrollierte Hitze und Druck zu dichten, festen Strukturen verbunden werden. Stellen Sie sich das Brennen von Keramik vor: Lose Tonpartikel verschmelzen unter hohen Temperaturen zu einer starren, zusammenhängenden Struktur. Ebenso ermöglicht Sintern die Verbindung von Metall- oder Keramikpulvern auf atomarer Ebene, wodurch Materialien mit verbesserten mechanischen und magnetischen Eigenschaften entstehen.
Wichtige Erkenntnis: Sintern ist nicht nur Erhitzen – es ist eine strategische Abstimmung von Temperatur, Zeit und Atmosphäre zur Optimierung der Atomdiffusion und Kornbindung.
Warum ist Sintern für NdFeB-Magnete unerlässlich?
NdFeB-Magnete, hauptsächlich bestehend ausNeodym (Nd), Eisen (Fe) und Bor (B), verfügen über außergewöhnliche magnetische Eigenschaften - hohe Remanenz (Br), Koerzitivfeldstärke (Hcb), UndEnergieprodukt (BHmax)Diese Eigenschaften machen sie in der modernen Technologie unverzichtbar. Ihre komplexe Zusammensetzung und Kristallstruktur stellen jedoch besondere Herausforderungen bei der Herstellung dar. Traditionelle Methoden wie Gießen oder Schmieden reichen nicht aus, da sie die erforderliche Präzision und Leistung nicht erreichen.
Sintern in Kombination mit Pulvermetallurgie bietet die perfekte Lösung. Durch die Aufteilung des Prozesses in überschaubare Schritte – beginnend mit den Rohstoffen und endend mit dem fertig geformten Magneten – stellt das Sintern sicher, dass NdFeB-Magnete ihr optimales magnetisches Potenzial erreichen. Es ist der Grundstein ihrer Produktion und schließt die Lücke zwischen Rohstoffen und fertigen Produkten.
Der Vorsinterprozess: Schritt für Schritt
Die Herstellung eines NdFeB-Magneten beginnt lange vor dem Anheizen des Sinterofens. Die Vorsinterphasen – Schmelzen, Mahlen und Formen – sind entscheidend für die Vorbereitung des Materials auf seine endgültige Umwandlung. Lassen Sie uns Schritt für Schritt vorgehen.
1. Schmelzen: Die perfekte Legierung herstellen
Der Prozess beginnt mit Präzision. Rohstoffe – Neodym, Eisen, Bor und Spuren von Elementen wieDysprosium (Dy), Niob (Nb) oder Kupfer (Cu) – werden sorgfältig abgemessen und gemischt. Die typische Zusammensetzung beträgt etwa 29–32,5 % Neodym, 63,95–68,65 % Eisen und 1,1–1,2 % Bor, mit geringfügigen Zusätzen zur Leistungssteigerung.
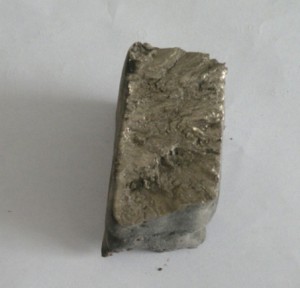
Pr-Nd
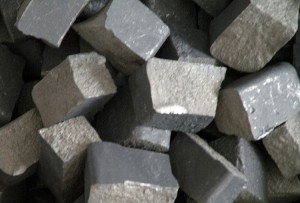
Dy-Fe
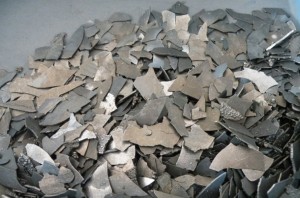
Co
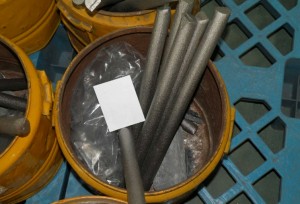
Fe
Diese Materialien werden anschließend in einem Vakuum-Induktionsofen bei Temperaturen zwischen 1400 und 1550 °C geschmolzen. Das Vakuum verhindert Verunreinigungen durch Sauerstoff oder andere Fremdstoffe und gewährleistet so eine reine Legierung. Nach dem Schmelzen wird die flüssige Legierung auf eine sich schnell drehende Kupferwalze gegossen und bei einer Gießtemperatur von 1380 bis 1510 °C zu dünnen Flocken (0,2 bis 0,45 mm dick) abgekühlt. Durch die schnelle Erstarrung entsteht eine gleichmäßige Kristallstruktur, die die Grundlage für den nächsten Schritt bildet.
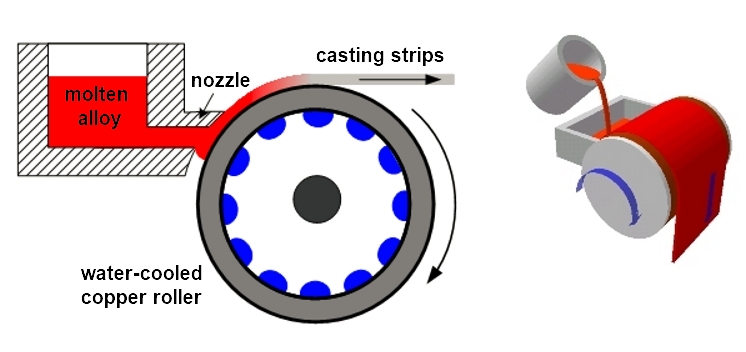
Schmelzverfahren
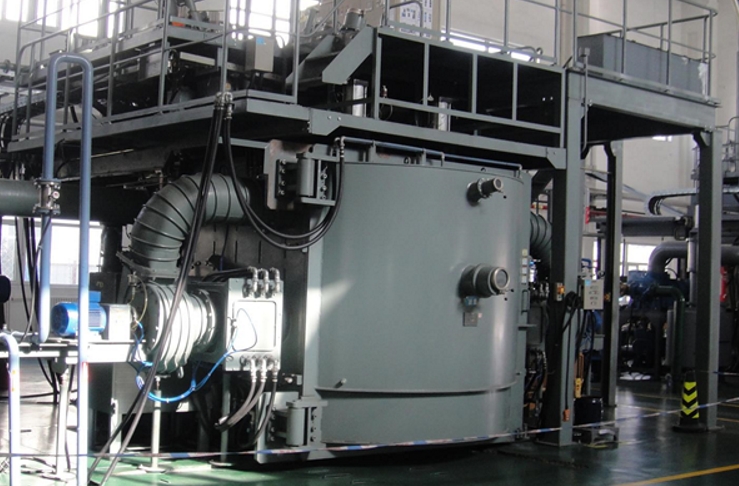
Vakuumofen
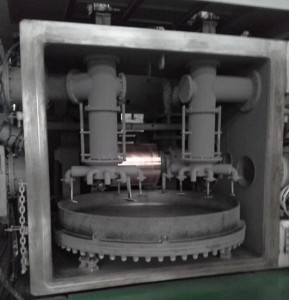
Innenvakuumofen
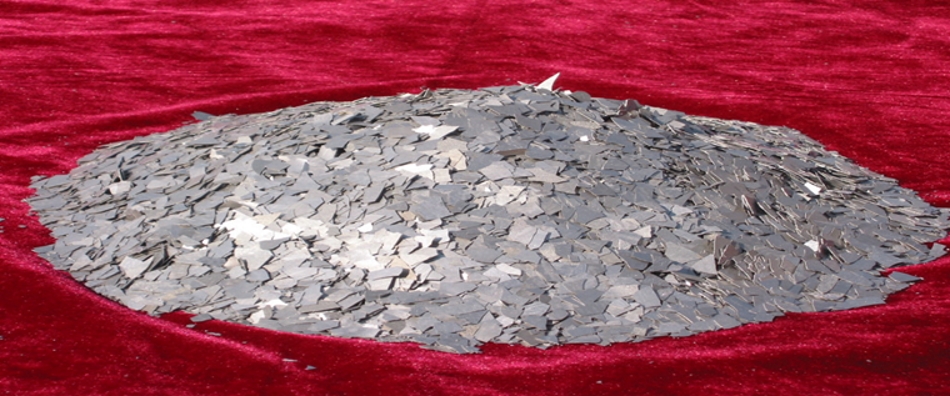
Gussstreifen
2. Mahlen: Von Flocken zu feinem Pulver
Anschließend werden die Legierungsflocken zu feinem Pulver verarbeitet – ein entscheidender Schritt für die endgültigen Eigenschaften des Magneten. Dieser Mahlprozess erfolgt in zwei Phasen:
• Wasserstoffdekrepitation (HD): Bei dieser raffinierten Technik werden die Flocken mithilfe von Wasserstoffgas zerkleinert. Die Legierung absorbiert Wasserstoff, wodurch sie sich ausdehnt und entlang ihrer neodymreichen Phasen bricht. Das Ergebnis? Grobes Pulver, bereit für die weitere Verfeinerung. HD ist effizient und erzeugt kleinere, gleichmäßigere Körner (typischerweise <10 μm), was die Koerzitivfeldstärke und Korrosionsbeständigkeit im Vergleich zur herkömmlichen mechanischen Zerkleinerung erhöht.
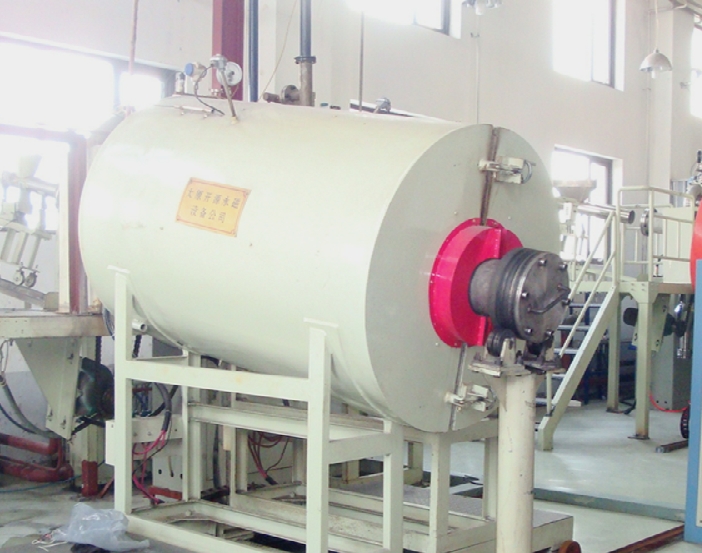
Wasserstoff-Entkrepitationsofen
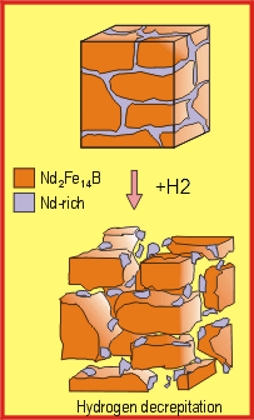
HD-Methode
• Strahlmahlen: Das grobe Pulver wird dann in eine Strahlmühle gegeben, wo Hochdruckgasströme die Partikel mit hoher Geschwindigkeit zusammenstoßen lassen. Dadurch wird das Pulver auf eine feine Größe von üblicherweise 2,8–3,5 μm mit gleichmäßiger Verteilung gemahlen. Je feiner das Pulver, desto besser die magnetischen Eigenschaften – allerdings steigt auch das Oxidationsrisiko, daher wird eine kleine Menge Luft zugeführt, um die Partikel zu passivieren.
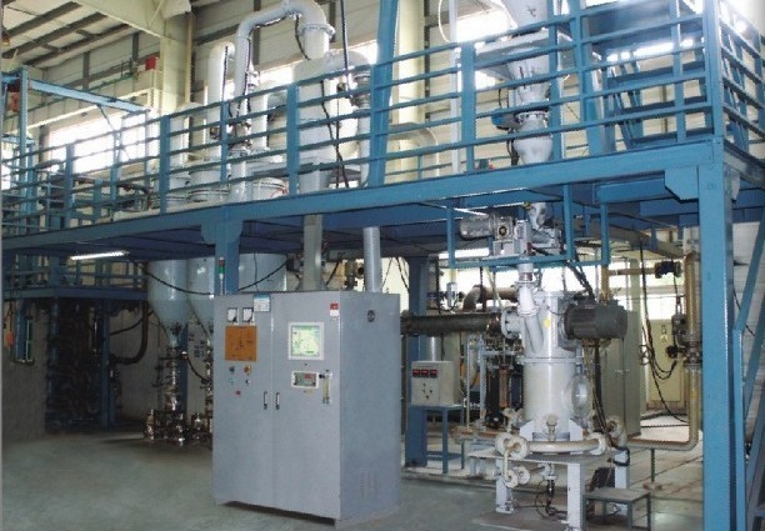
Strahlfräsmaschine
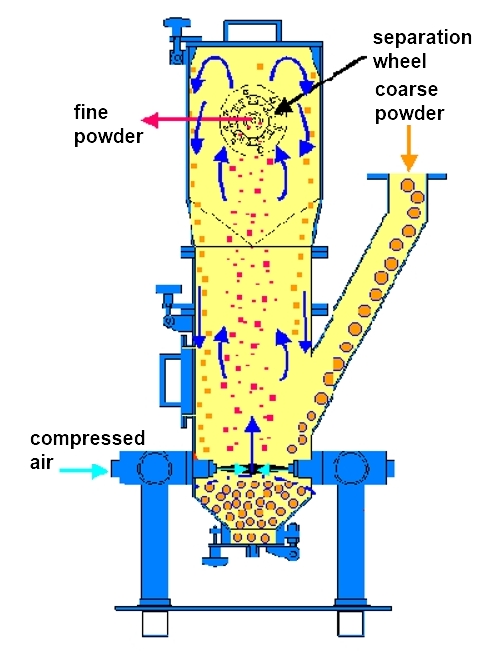
Strahlmahlverfahren
3. Pressen: Formgebung des Magnetrohlings
Nachdem das Pulver vorbereitet ist, wird dem Magneten seine Form gegeben. In diesem Schritt wird das Pulver mithilfe von Formen, die auf die gewünschte Geometrie zugeschnitten sind – Zylinder, Würfel, Kacheln oder Ringe, je nach Anwendung – zu einem kompakten, sogenannten „Grünling“ gepresst.
• Magnetfeldpressen: Das Pulver wird unter einem Magnetfeld gepresst, um die magnetischen Domänen der Partikel auszurichten. Diese Ausrichtung ist entscheidend für die maximale Magnetstärke. Der Druck verdichtet das Pulver zu einem zerbrechlichen Rohling mit einer Dichte von etwa 4,0–4,2 g/cm³.
• Isostatisches Pressen: Für eine noch gleichmäßigere Formgebung wird der Rohling isostatisch gepresst. In Hydrauliköl getaucht, wird er einem Druck ausgesetzt, der seine Dichte auf 4,5–4,9 g/cm³ erhöht. Dieser Schritt stellt sicher, dass der Rohling robust und gleichmäßig gepackt ist und zum Sintern bereit ist.

Pressmaschine
4. Sintern: Vorbereitungen für das Sintern
Am Ende des Vorsinterprozesses hatte der NdFeB-Rohling zwar Gestalt angenommen, war aber noch eine fragile, poröse Struktur mit ungenutztem Potenzial. Im nächsten Schritt – dem Sintern – wird er in einem Vakuumofen auf 1050–1150 °C erhitzt, wodurch die Partikel zu einem dichten Hochleistungsmagneten verschmolzen werden. Anschließend erfolgt eine Alterung (500–900 °C), um die Mikrostruktur zu verfeinern und die Koerzitivfeldstärke zu erhöhen.
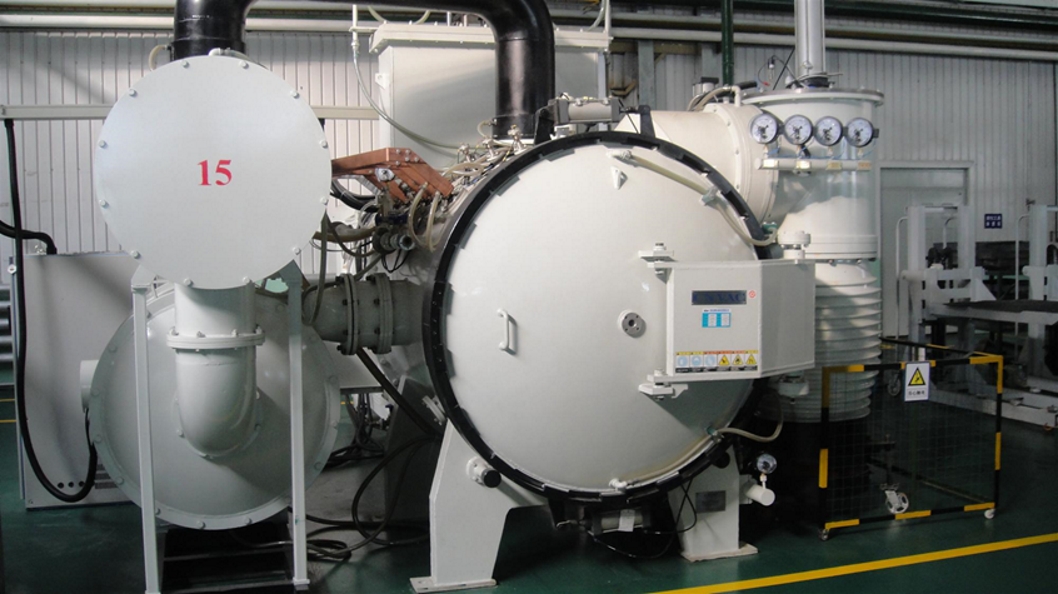
Vakuum-Sinterofen
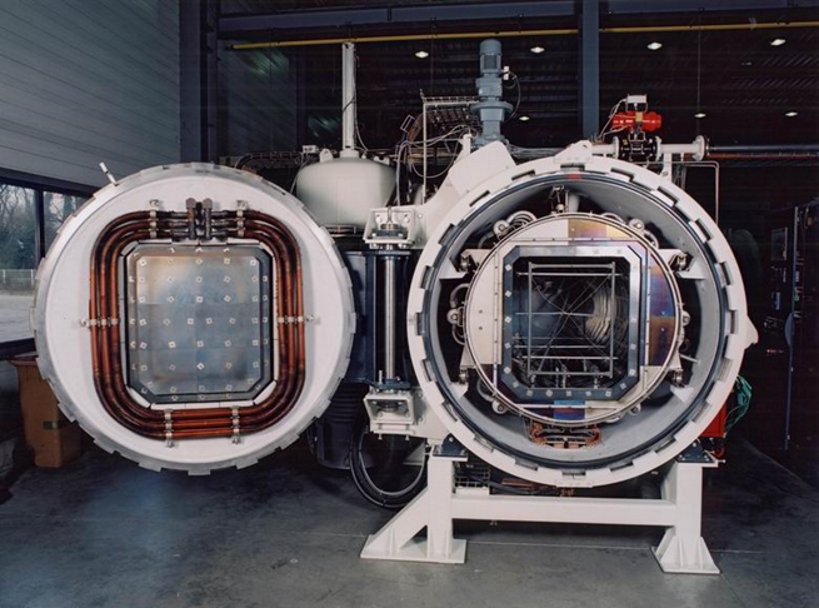
Innensinterofen
Zusammen bilden diese Vorsinterschritte – Schmelzen, Mahlen und Pressen – die Grundlage für die Herstellung von NdFeB-Magneten. Jeder Schritt ist ein anspruchsvolles Gleichgewicht zwischen Wissenschaft und Technik, das sicherstellt, dass aus den Rohstoffen ein Rohling entsteht, der seine magnetische Kraft entfaltet.
Qualitätssicherung: Exzellenz sicherstellen
Jeder gesinterte Rohling wird strengen Tests unterzogen:
• Maßgenauigkeit: Gemessen mit einem Koordinatenmessgerät (CMM).
• Dichte: Auswertung nach dem Archimedes-Prinzip.
•Magnetische Eigenschaften: Mit BH-Analysatoren getestet, um Br, Hcj und (BH)max zu überprüfen.
• Mikrostrukturanalyse: SEM/TEM-Bildgebung bewertet Korngröße und Phasenverteilung.
• Umweltbeständigkeit: Salzsprühnebel- und Temperaturwechseltests bestätigen die Korrosions- und Temperaturbeständigkeit.
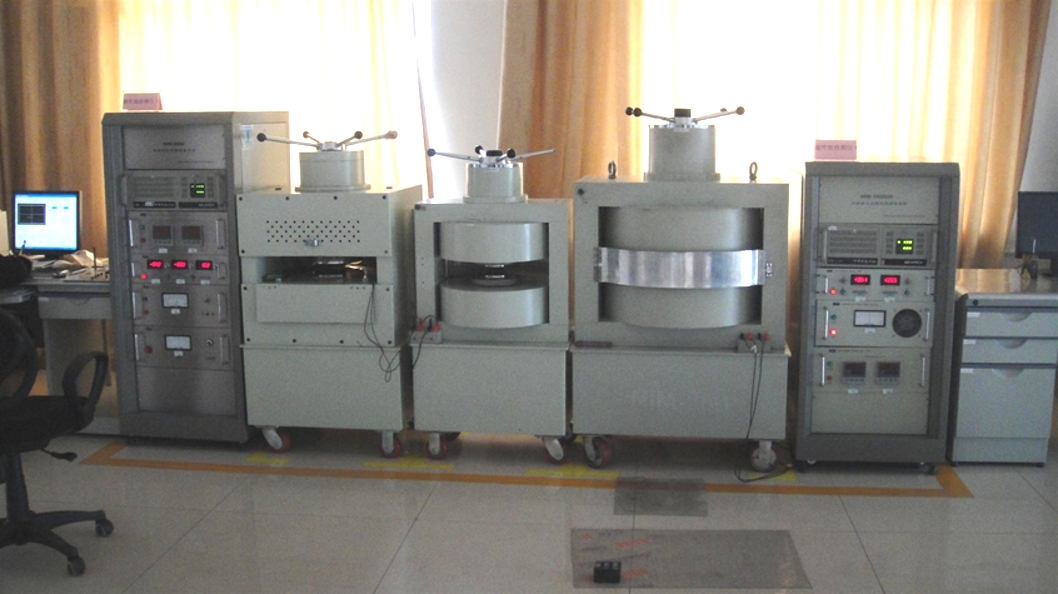
Hysterese-Schleifentaster
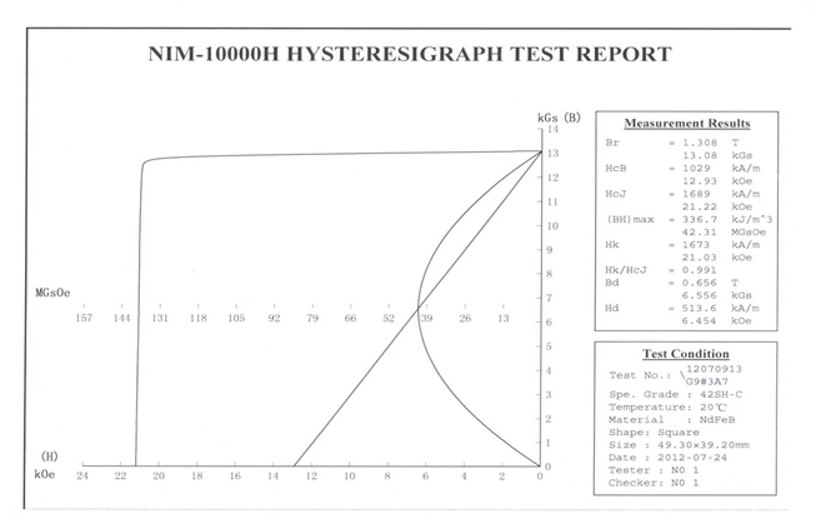
Hystereseschleife
Der Vorsinterprozess ist nicht ohne Hürden. Eine präzise Kontrolle der Pulvergröße, des Sauerstoffgehalts und der Pressbedingungen ist unerlässlich, um Defekte wie Porosität oder ungleichmäßige Dichte zu vermeiden. Fortschritte wie Wasserstoffdekrepitation und Strahlmahlen haben Effizienz und Qualität verbessert, während laufende Forschungen nach Möglichkeiten suchen, den Seltenerdgehalt ohne Leistungseinbußen zu reduzieren – ein Hinweis auf Nachhaltigkeit in der Magnetproduktion.
Der Vorsinterprozess von NdFeB-Magneten zeugt vom Einfallsreichtum der modernen Materialwissenschaft. Von der geschmolzenen Legierung bis zum fein geformten Rohling – jeder Schritt führt zur Herstellung von Magneten, die unsere Welt mit Energie versorgen. Ob Technikbegeisterter oder Branchenprofi: Das Verständnis dieses Prozesses offenbart die verborgene Handwerkskunst hinter alltäglichen Innovationen.
Bei AIC Magnetics kombinieren wir jahrzehntelange Erfahrung im Bereich magnetischer Materialien mit modernster Sintertechnologie, um maßgeschneiderte NdFeB-Lösungen für Ihre Bedürfnisse zu entwickeln. Kontaktieren Sie uns und erfahren Sie, wie unsere Magnete Ihren nächsten Durchbruch ermöglichen können.
Veröffentlichungszeit: 27. Februar 2025