Permanent magnet materials are magnetic materials that can generate a magnetic field permanently, without the need for external energy input. They offer many advantages, such as energy efficiency and convenience. In particular, rare earth magnet materials, characterized by high coercivity and high magnetic energy products, allow the use of smaller and thinner magnet sizes in device magnetic circuits to achieve product functionality, greatly promoting the miniaturization and lightweight design of permanent magnet devices. As indispensable functional materials in the field of high technology, permanent magnet materials are widely used in many fields, including aerospace, defense, electronics and telecommunications, transportation, industrial energy, and household appliances.
According to their working principles, the applications of permanent magnets can be classified into five types:
Function | Principle | Physical law | Typical Application |
Electrical energy converts into mechanical energy | The effect of magnetic fields on current-carrying conductors | Ampere's law | Speakers, motors, headphones, measuring instruments |
Mechanical energy converts into electrical energy | Motion of conductor relative to magnetic field produces induced electromotive force | Faraday's law | Generator, Microphone, Sensor |
Conversion of mechanical energy | Interaction between the poles of a permanent magnet, between permanent magnet and ferromagnetic substance | Coulomb's law | Magnets for adsorption, magnetic separators, magnetic filters, magnetic couplings, permanent magnetic chuck |
Various magnetic effects | Between magnetic fields and light, electricity, heat, etc. | Nuclear Magnetic Resonance, Oscillator, Optical Isolator | |
Other magnetic applications | The effect of magnetic fields on charged particles | Lorentz's law | magnetrons, particle gas pedals, magnetic spectrometers, magnetron sputtering, electrical switches |
Permanent magnet materials are widely used, and in the early stages of engineering development, choosing the right permanent magnet material is a consideration for every engineer. Each type of permanent magnet material has its own unique characteristics, so selecting a permanent magnet involves considering multiple factors, such as the required magnetic field strength, temperature resistance, cost, and manufacturing processes. We suggest following these steps:
(1) Determine magnetic field strength requirements
Throughout the system or device, permanent magnets are primarily used as functional components (rather than aesthetic or structural parts) to provide a passive magnetic field. Magnetic field strength is a key indicator of magnetic steel performance and a core element in engineering design. How to maximize the use of the magnetic field strength of permanent magnets is also a basic goal in the design of permanent magnet devices. Engineers can calculate the target magnetic field strength and use this as the basis for subsequent material selection.
(2) Select suitable magnetic materials
Common permanent magnet materials used in engineering include sintered neodymium-iron-boron (NdFeB), sintered samarium cobalt (SmCo), sintered or cast alnico (aluminum-nickel-cobalt), sintered ferrite, bonded and injection molded magnets, and a few newer materials such as samarium iron nitride (SmFeN). Different permanent magnet materials have their own magnetic properties and material characteristics.
Grade | Br/kGs | Hcb/kOe | Hcj/kOe | (BH)max/MGOe | Tmax(℃)* | |
Sintered NdFeB Magnets | 42SH | 12.5 | 12.3 | 21 | 42 | <150 |
Sintered SmCo Magnets | 28 | 10.8 | 9.8 | 22 | 28 | <300 |
Sintered/Casted AlNiCo Magnets | CLNG44 | 12.5 | 0.65 | 0.65 | 5.5 | <525 |
Hard Ferrite Magnets | Y30 | 4 | 2.6 | 2.7 | 3.7 | <250 |
Bonded Magnets | CMN10 | 7.2 | 6 | 10 | 10 | <150 |
Injection Molded Magnets | IMF0606 | 2.9 | 2.2 | 3.2 | 2.2 | <140 |
*The maximum operating temperatures are for reference only. | ||||||
The actual maximum operating temperature of permanent magnet depends on the grade, shape, and magnetic circuit. |
(3) Clarify the specifications and dimensions of the magnet
For achieving a certain magnetic field strength, different permanent magnets require different sizes. The specifications and shapes of permanent magnets depend on the specific requirements of the actual application, combined with factors such as spatial constraints and magnetic field direction, to determine the appropriate size and shape.
The image on the right compares the amount of permanent magnet material needed to attract a 5KG iron block. For example, sintered neodymium-iron-boron (NdFeB) requires only D20x5mm, while sintered ferrite requires D20x55mm, which is more than ten times the amount required by NdFeB.
(4) Assess the machinability of the magnet
Assess the machinability of the magnet: Conventional production processes for permanent magnet materials mainly include sintering, casting, and molding. Among these, sintered and cast permanent magnet materials are hard and brittle with poor toughness and machinability. They are usually made into blanks first, then shaped using wire cutting, slicing, and grinding processes. They cannot be processed with machining techniques such as turning, milling, or planing, and conventional products are mostly in simple shapes such as plates, rings, or tiles. If designed in complex shapes or high precision, special processes are required, which can be costly. These processing factors need to be considered in the early design of the product.
The table on the right compares the material properties of conventional permanent magnet materials.
Density g/cm3 | Hardness Hv | Bend Strength MPa | |
Sintered NdFeB Magnets | 7.5-7.8 | 400-600 | 250-300 |
Sintered SmCo Magnets 2:17 | 8.3-8.5 | 550-600 | 120-150 |
Casted AlNiCo Magnets | 6.9-7.3 | 520-700 | 50-310 |
Hard Ferrite Magnets | 4.9-5.1 | 400-700 | 50-90 |
Bonded Magnets | 5.5-6.4 | 80-120 | 100-160 |
Injection Molded Magnets | 3-5.5 | 140-150 | 60-100 |
Rubber Magnets | 3.5-3.7 | / | / |
(5) Consider working environment factors
The working environment of a permanent magnet has a significant impact on its performance and lifespan. Exposure to temperature, humidity, and corrosive materials can negatively affect the magnet, and it is important to ensure that the chosen magnetic material can adapt to the actual application environment.
The image on the right shows a comparison of the applicable operating temperature ranges for conventional permanent magnet materials. Neodymium-iron-boron (NdFeB) and ferrite have narrower working temperature ranges, while samarium-cobalt (SmCo) and alnico (aluminum-nickel-cobalt) have a wider working temperature range.
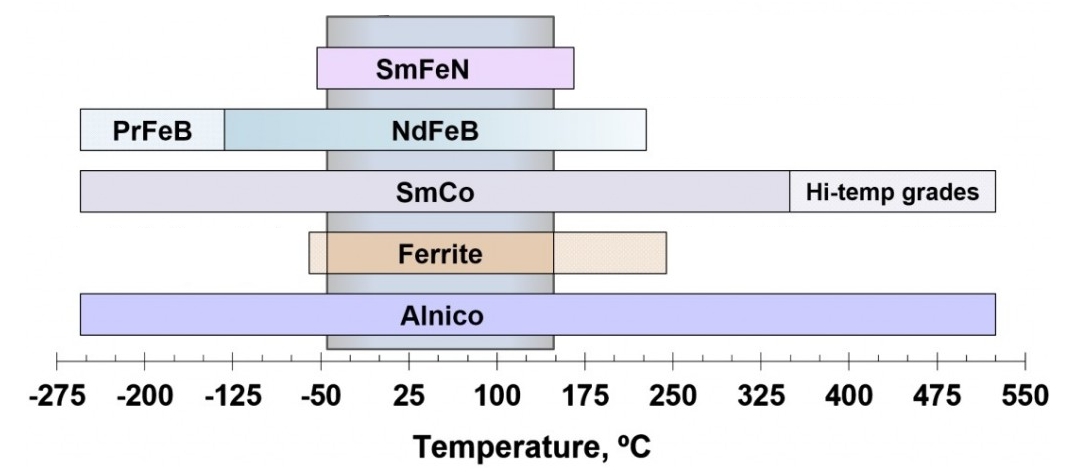
(6) Weighing material costs
Weighing material costs: The costs of different types of permanent magnet materials vary greatly, so it is important to consider them thoroughly to ensure that project costs are controlled while meeting performance requirements.
The image on the right shows a price comparison of conventional permanent magnet materials for D10x10mm disc products (numbers represent a comparative indication of price differences, not actual product prices). Sintered samarium cobalt is the most expensive, while sintered ferrite is the least expensive.
(7) Pay attention to other special requirements
Pay attention to other special requirements: Some application scenarios may have specific requirements for magnets, such as high coercivity, high residual magnetism, or low temperature coefficients. In such cases, we recommend that you contact us to discuss and evaluate these specific requirements.
Based on the above factors, a summary comparison of the performance and characteristics of various permanent magnet materials is made as follows:
Magnetic Property | Processability | Working Temperature | Corrosion Resistance | Stability | Cost | |
Sintered NdFeB Magnets | Highest, (BH)max 35-52MGOe | Brittle texture, high hardness, not easy to process | Not resistant to high temperature, the working temperature should not exceed 200℃ | Easy to corrode, need plating protection | Good | High and unstable |
Sintered SmCo Magnets | Higher, (BH)max 17-30MGOe | Brittle texture, high hardness, not easy to process | High temperature resistance, working temperature up to 350°C | Good corrosion resistance | Excellent | High |
Casted AlNiCo Magnets | Average, (BH)max < 9MGOe | Brittle texture, high hardness, not easy to process | High temperature resistance, working temperature up to 550°C | Good corrosion resistance | easy demagnetization | Moderate |
Hard Ferrite Magnets | Lower, (BH)max < 4MGOe | Brittle texture, high hardness, not easy to process | General performance, working temperature up to 250℃ | Good corrosion resistance | Average stability, better than AlNiCo | Low |
Bonded Magnets | Average, (BH)max 2-14MGOe | Complex shapes can be made through molds | Not resistant to high temperature, the working temperature should not exceed 150℃ | Easy to corrode, need plating protection | Good | Moderate |
Injection Molded Magnets | Lower, (BH)max < 10MGOe | Complex shapes can be made through molds | Not resistant to high temperature, the working temperature should not exceed 120℃ | Good corrosion resistance | Good | Low price, High Mold cost |
Based on the above factors, a preliminary selection of permanent magnet materials can be made according to the following table:
Material | Price | Magnetic Property | Temperature Resistance | Operating Environment | Processability | Corrosion Resistance | |||||
Magnetic Field | Magnetic Attraction | Heat-resistant | Cold-resistant | Outdoor | Underwater | Machining Precision | Complex Shape | Mechanical Strength | |||
Sintered NdFeB Magnets | Δ | √ | √ | Δ | √ | × | × | × | × | Ο | Δ |
Sintered SmCo Magnets | × | √ | √ | √ | √ | √ | √ | × | × | Δ | √ |
Casted AlNiCo Magnets | Ο | Δ | Δ | √ | √ | √ | √ | × | × | √ | √ |
Hard Ferrite Magnets | √ | × | × | Ο | × | √ | √ | × | × | × | √ |
Bonded Magnets | Ο | Δ | Δ | Δ | √ | × | × | × | × | × | Δ |
Injection Molded Magnets | Ο | Δ | Δ | Δ | √ | √ | √ | √ | √ | × | √ |
√······Excellent Ο······Good Δ······Average ×······Poor, Comparison of products based on the same size and direction of magnetization. |
When choosing permanent magnet materials, please consider all the above factors according to the needs of your engineering project and select the appropriate permanent magnet material. If you have any questions during the evaluation process, please contact us. We are committed to providing you with professional advice and comprehensive support.